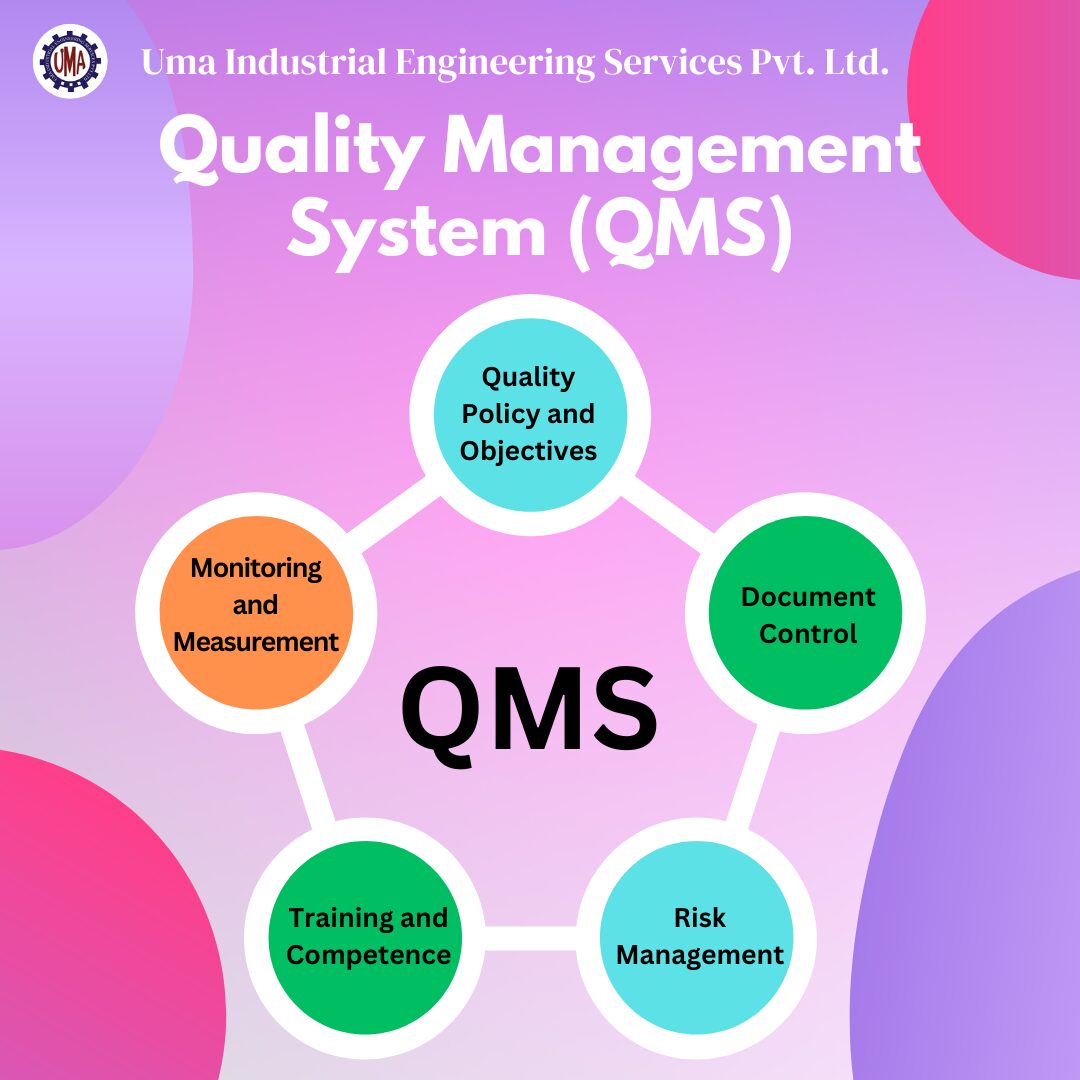
Mastering Quality: The Essentials of Quality Management Systems (QMS)
In the fast-paced world of industry and business, achieving and maintaining high-quality standards is paramount. A Quality Management System (QMS) emerges as the cornerstone in ensuring products and services consistently meet or exceed customer expectations. In this comprehensive guide, we’ll delve into the core aspects of QMS, its significance, the diverse types available, and the steps to effectively implement it.
What is a Quality Management System (QMS)?
A Quality Management System (QMS) is a structured framework designed to manage and improve the quality of products and services within an organization. It’s a holistic approach that integrates various processes, policies, and objectives to meet customer expectations and regulatory requirements consistently.
Core Elements of a Quality Management System (QMS)
A well-established QMS comprises several essential elements, each contributing to the overall effectiveness of the system.
1. Quality Policy and Objectives:
A documented quality policy and measurable objectives set the tone for the organization’s commitment to quality. This provides a clear roadmap for everyone in the organization.
2. Document Control:
Effective document control ensures that the right documents are available to the right people at the right time. This includes procedures, manuals, and records.
3. Risk Management:
Identifying and managing risks is integral to preventing issues that could impact quality. A robust QMS incorporates risk management strategies to enhance decision-making.
4. Training and Competence:
Ensuring that personnel have the necessary skills and knowledge is crucial. Training programs and competency assessments form a part of QMS to maintain a qualified workforce.
5. Monitoring and Measurement:
Regular monitoring and measurement of processes help in identifying areas for improvement. This includes the use of key performance indicators (KPIs) to track progress.
Why is Quality Management System (QMS) Important?
Implementing a QMS is not just a choice; it’s a strategic imperative for organizations aiming for sustained success. Here’s why:
1. Enhanced Customer Satisfaction:
By consistently delivering high-quality products or services, customer satisfaction is maximized, leading to loyalty and positive word-of-mouth.
2. Compliance with Regulations:
QMS ensures that products and processes adhere to regulatory standards, reducing the risk of legal issues and ensuring a smoother path to market.
3. Continuous Improvement:
QMS fosters a culture of continuous improvement by providing a systematic framework for evaluating processes and implementing enhancements.
4. Increased Operational Efficiency:
Streamlined processes and a focus on efficiency contribute to reduced waste, fewer defects, and increased productivity.
5. Market Competitiveness:
Organizations with a certified QMS often gain a competitive edge in the market. Many clients and partners prefer working with businesses committed to quality.
Benefits of Quality Management Systems
1. Consistency in Quality:
QMS ensures consistency in delivering high-quality products or services, reducing variability and customer complaints.
2. Cost Efficiency:
By minimizing errors and defects, QMS contributes to cost savings associated with rework and warranty claims.
3. Employee Engagement:
Clear processes and defined responsibilities lead to increased employee engagement and a shared commitment to quality.
4. Brand Reputation:
A strong QMS enhances a brand’s reputation, fostering trust among customers, partners, and stakeholders.
How to Implement a Quality Management System (QMS)
Implementing a QMS is a strategic initiative that involves the following key steps:
1. Leadership Commitment:
The commitment of top leadership is crucial. Leaders must champion the QMS implementation, communicating its importance throughout the organization.
2. Define Objectives and Processes:
Clearly define the organization’s objectives and the key processes involved. This forms the foundation for the QMS.
3. Employee Training:
Train employees on the QMS, ensuring they understand their roles, responsibilities, and the importance of quality in their work.
4. Document Processes:
Documenting processes, procedures, and work instructions ensures consistency and provides a reference for employees.
5. Implement and Monitor:
Roll out the QMS, and continually monitor its effectiveness. Use key performance indicators to assess progress and identify areas for improvement.
6. Internal Audits:
Conduct internal audits regularly to evaluate the QMS’s effectiveness and identify opportunities for improvement.
7. Certification (Optional):
While not mandatory, obtaining certification from recognized bodies like ISO can enhance the credibility of the QMS.
In conclusion, a well-implemented QMS is not just a checkbox for compliance; it’s a strategic investment in quality, efficiency, and the long-term success of an organization. Whether adopting a standard like ISO 9001 or utilizing methodologies like Six Sigma, organizations can tailor their QMS to their unique needs, ensuring a culture of continuous improvement and excellence. Through its systematic approach, a QMS becomes the cornerstone of organizational success, ensuring that quality is not just a goal but a way of doing business.